Plastic extrusion for creating standardized, high-quality parts
A Comprehensive Guide to the Refine and Benefits of Plastic Extrusion
In the vast world of manufacturing, plastic extrusion becomes a important and extremely efficient procedure. Translating raw plastic right into continuous profiles, it satisfies a huge selection of markets with its exceptional adaptability. This overview intends to illuminate the elaborate actions involved in this approach, the types of plastic apt for extrusion, and the game-changing benefits it brings to the industry. The following conversation guarantees to unfold the real-world impacts of this transformative process.
Comprehending the Basics of Plastic Extrusion
While it may appear complex at first glimpse, the procedure of plastic extrusion is essentially simple. The process begins with the feeding of plastic product, in the type of powders, granules, or pellets, into a warmed barrel. The designed plastic is then cooled, strengthened, and reduced into desired sizes, completing the procedure.
The Technical Process of Plastic Extrusion Explained

Kinds Of Plastic Suitable for Extrusion
The choice of the appropriate kind of plastic is a crucial aspect of the extrusion process. Numerous plastics offer unique residential or commercial properties, making them a lot more fit to certain applications. Polyethylene, for instance, is generally used because of its reduced price and simple formability. It provides exceptional resistance to chemicals and moisture, making it perfect for items like tubing and containers. Polypropylene is an additional prominent option due to its high melting point and resistance to tiredness. For even more robust applications, polystyrene and PVC (polyvinyl chloride) are frequently selected for their stamina and durability. These are common alternatives, the selection eventually depends on the details needs of the product being generated. Recognizing these plastic types can dramatically enhance the extrusion process.
Comparing Plastic Extrusion to Other Plastic Forming Methods
Comprehending the kinds of plastic suitable for extrusion paves the method for a broader discussion on exactly how plastic extrusion stacks up against other plastic developing techniques. Plastic extrusion is unequaled when it comes to developing constant accounts, such as pipelines, seals, and gaskets. It likewise permits for a regular cross-section along the length of the product.
Secret Benefits of Plastic Extrusion in Production
In the realm of production, plastic extrusion provides lots of significant benefits. One significant advantage is the cost-effectiveness of the process, that makes it an economically enticing production approach. Additionally, this strategy provides premium product flexibility and improved manufacturing rate, consequently boosting general manufacturing effectiveness.
Cost-Effective Manufacturing Method
Plastic extrusion leaps to the forefront as an economical production approach in production. Furthermore, plastic extrusion needs less power than traditional production methods, contributing to reduced functional expenses. On the whole, the economic advantages make plastic extrusion a very attractive choice in the manufacturing market.
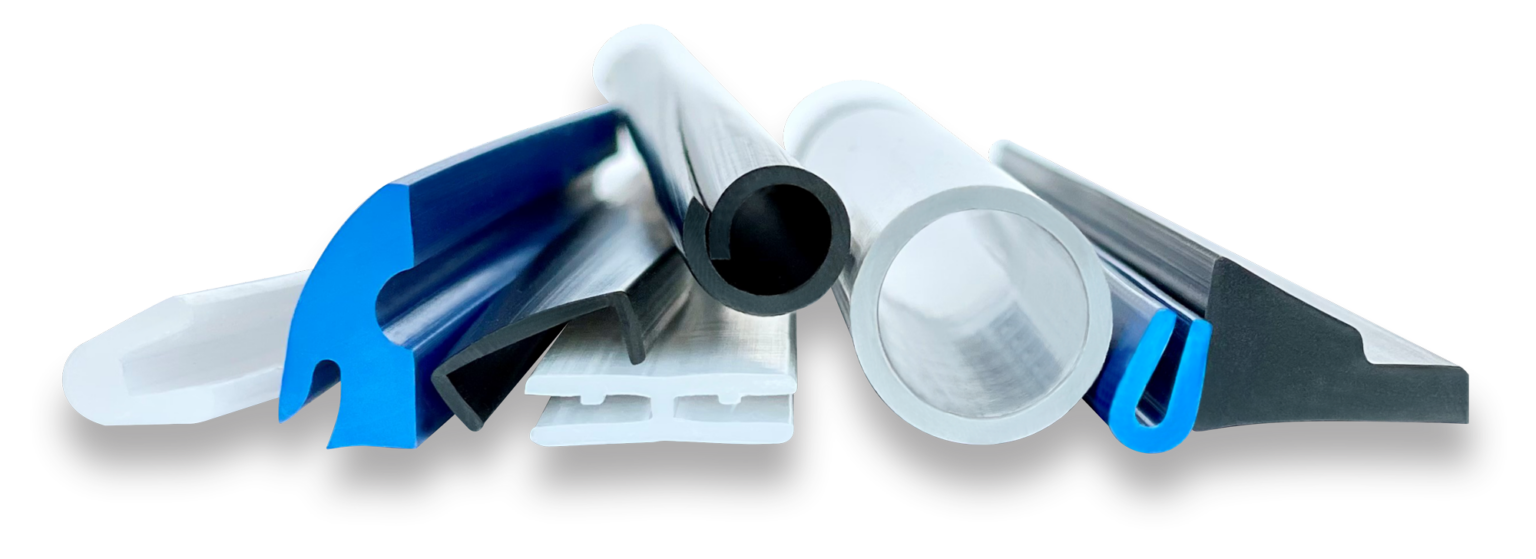
Superior Product Adaptability
Past the cost-effectiveness of plastic extrusion, an additional considerable advantage in producing lies in its exceptional product adaptability. This process permits for the creation of a wide range of items find more information with differing sizes, styles, and forms, from easy plastic sheets to complex accounts. The adaptability is credited to the extrusion die, which can be personalized to yield the wanted product style. This makes plastic extrusion an optimal service for sectors that need tailored plastic elements, such as automobile, building and construction, and product packaging. The ability to generate varied products is not only valuable in conference particular market needs yet also in allowing producers to discover new line of product with minimal capital expense. In significance, plastic extrusion's product flexibility cultivates advancement while boosting functional efficiency.
Improved Production Speed
A significant advantage of plastic extrusion depends on its boosted production rate. This manufacturing procedure enables high-volume production in a reasonably short time period. It is capable of creating long, continuous plastic profiles, which substantially lowers the manufacturing time. This high-speed production is specifically useful in sectors where large quantities of plastic parts are needed within limited target dates. Few various other production processes can match the rate of plastic extrusion. Additionally, the ability to preserve consistent high-speed production without giving up item high quality sets plastic extrusion apart from other approaches. The boosted production rate, for that reason, not just enables producers to meet high-demand orders yet additionally contributes to enhanced efficiency and cost-effectiveness. This useful function of plastic extrusion has made it a favored choice in various sectors.
Real-world Applications and Effects of Plastic Extrusion
In the realm of production, the method of plastic extrusion holds extensive relevance. The financial advantage of plastic extrusion, largely its high-volume and cost-efficient output, has actually transformed production. The industry is persistently striving for innovations in recyclable and eco-friendly materials, showing a future where the advantages of plastic extrusion can be preserved without endangering ecological sustainability.
Verdict
Finally, plastic extrusion is a highly efficient and effective method of changing basic materials into diverse items. It offers various benefits over other plastic creating techniques, including cost-effectiveness, high outcome, minimal waste, anchor and design flexibility. Its influence is greatly really felt in different markets such as building and construction, vehicle, and consumer products, making it a crucial process in today's manufacturing landscape.
Digging deeper into the technological procedure of plastic extrusion, it begins with the choice of the proper plastic material. As soon as cooled down, the plastic is cut right into the needed lengths sites or wound onto reels if the product is a plastic film or sheet - plastic extrusion. Contrasting Plastic Extrusion to Other Plastic Forming Methods
Recognizing the kinds of plastic appropriate for extrusion paves the means for a broader conversation on exactly how plastic extrusion piles up against other plastic creating approaches. Few various other production procedures can match the speed of plastic extrusion.